Die neue Wintersaison steht vor der Tür. Was könnte da als Einstimmung besser sein, als sich das Fahrobjekt für den ersten Flockenfall mal eben selbst zu bauen. Ski, Snowboard, oder Splitboard – bei Build2Ride werdet ihr auf jeden Fall geholfen. Aus der gesamten Republik und selbst aus der Schweiz und Österreich reisen die Baufreudigen an, um dem persönlichen Traum vom eigenen Fahrgefährt den letzten, persönlichen Schliff zu geben.
Build2Ride wurde 2012 von Flo Baumgärtel (Werkstattleitung), der bereits für namhafte Sponsoren fuhr, dem ehemaligen Skirennläufer Axel Forelle (Marketing und Vertrieb) und Matthias Schmidlechner (Einkauf und Entwicklung) ins Leben gerufen. Seitdem erfreut sich das Unternehmen einer stetig steigenden Beliebtheit. 2013 stand dann noch ein ISPO BRANDNEW Award ins Haus, der die Einzigartigkeit des Angebots von Buil2Ride noch zusätzlich unterstreicht. Doch nicht nur Wintersportgeräte werden in der ehemaligen Schreinerei im oberbayerischen Farchant, kurz vor Garmisch-Partenkirchen, individuell gefertigt. Auch ein auf die eigene Physiognomie abgestimmtes Mountainbike wird auf Wunsch mit eigenen Grafix (unter Lack) und persönlich ausgesuchter Farbgebung versehen.
Build your Ride – as u like it
Die Ausrichter der Workshops sind Freerider wie man es sich nur wünschen kann. Als Garmisch-Locals wissen sie was gefordert ist im Gelände und auf der Piste. Und sie wissen auch worauf es beim Bau der „Snowwaffen“ ankommt. Unter fachkundiger und geduldiger Anweisung wird in holzduftiger Workshopatmosphäre gesägt, gefeilt, geschraubt und geshaped. Beim Blick aus dem Werkstattfenster grüßt die bereits verschneite Zugspitze, was die Vorfreude noch zusätzlich steigert. Im Vorfeld wird per Fragebogen oder ggf. per Telefonat besprochen, was die Workshop-Besucher konkret realisieren wollen und werden dank mehrjähriger Expertise der Inhaber bestens beraten. Bindungen jedweder Art, können über die guten Build2Ride-Kontakte im Vorhinein organisiert werden. Der eigenen Kreativität sind dabei kaum Grenzen gesetzt: Egal ob Grafikplots als Top- oder Bottomsheet, verschiedenste Holzfurniere, eure alten T-Shirts oder Buchstabensuppe – fast alles kann und wird beim Design von Boards und Ski umgesetzt. Und am Ende eines kurzweiligen Wochenendes steht es dann endlich vor euch – das Unikat eurer Träume. Ready2Ride durch eure eigenen Hände und Ideen. Build2Ride durch euer eigenes Können.
So entsteht (d)ein individuelles Splitboard bei Build2Ride
Die folgende Bildersequenz soll euch exemplarisch zeigen, wieviele und welche Arbeitsschritte über zwei Tage anfallen. So könnt Ihr euch besser vorstellen, was geht und was nicht – eines noch vorweg: Alle Schritte sind bei Snowboards und Ski fast identisch.
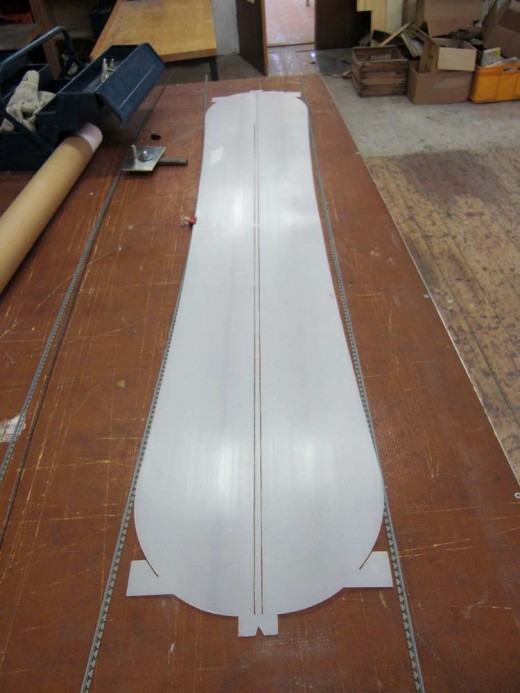
Step 1: Dem bereits zu Beginn vorliegenden, wassergestrahlten Belagrohling, wird die Kante angelegt © airFreshing.com
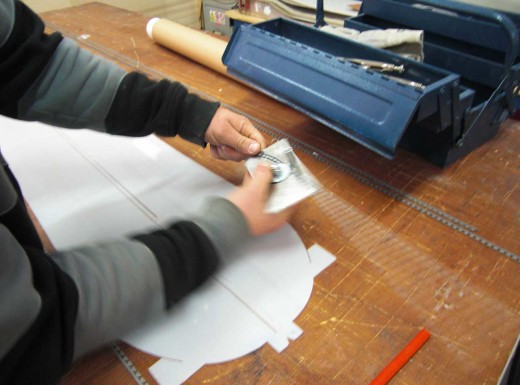
Step 2: Die Kante wird analog des Shapes vorgebogen © airFreshing.com
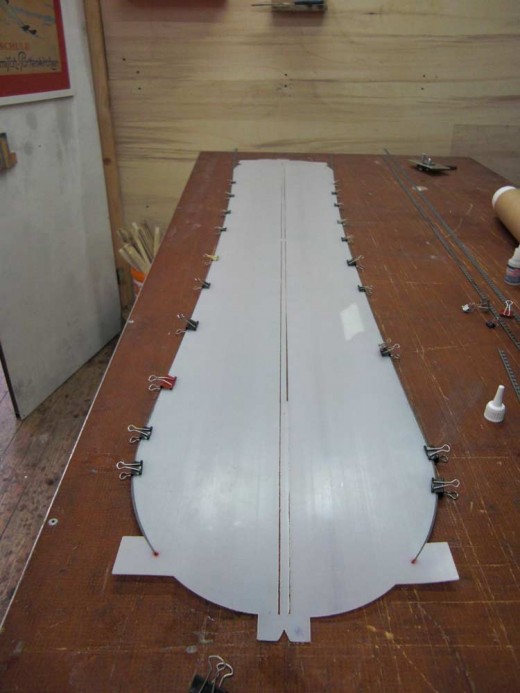
Step 3 : Die Kanten werden mittels Sekundenkleber in ihrer Position fixiert © airFreshing.com
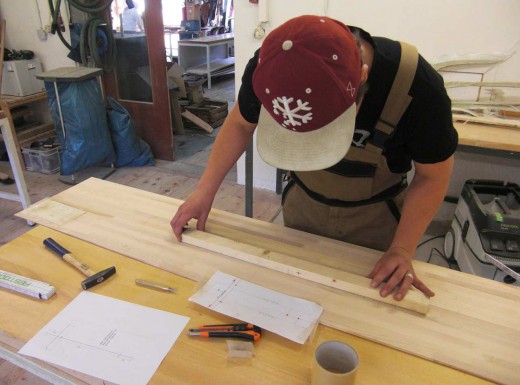
Step 4 : Jetzt kommen die Inserts an die Reihe, sie werden via Schablone angezeichnet © airFreshing.com
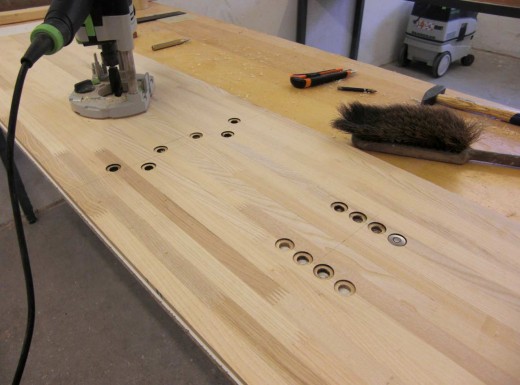
Step 5: Die Inserts werden mit der Oberfräse vorgebohrt © airFreshing.com
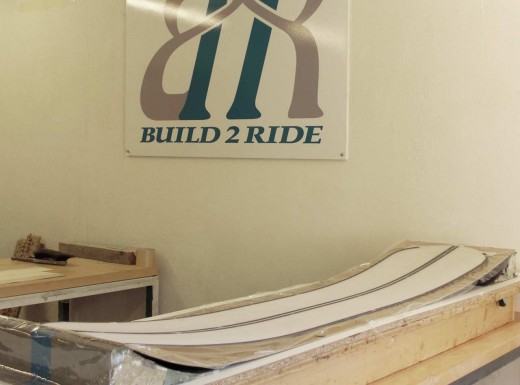
Step 6: Der Boardrohling wird in die vogesehene Form eingepasst © airFreshing.com
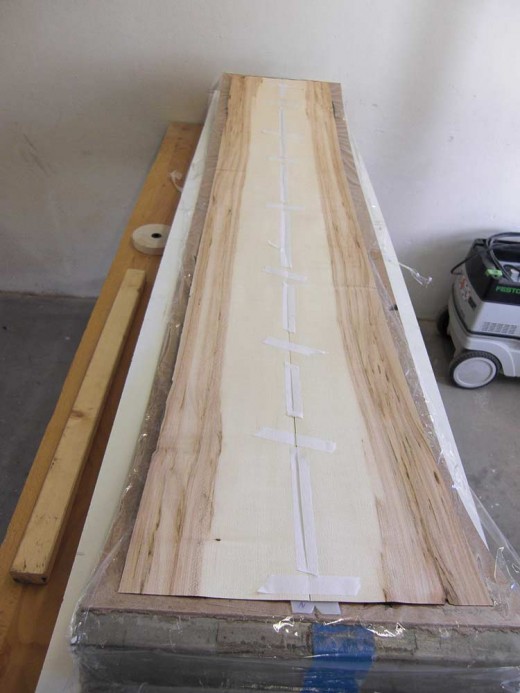
Step 7: Das Topsheet (In diesem Fall Furnier) wird angelegt © airFreshing.com
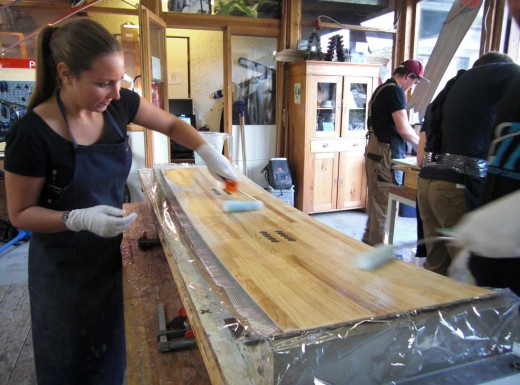
Step 8: Zeit für Harz! Die verschiedenen Schichten werden mit Epoxidharz gewalzt und so verbunden © airFreshing.com

Step 9: Der Vakuumschlauch wird vorsichtig übergezogen © airFreshing.com
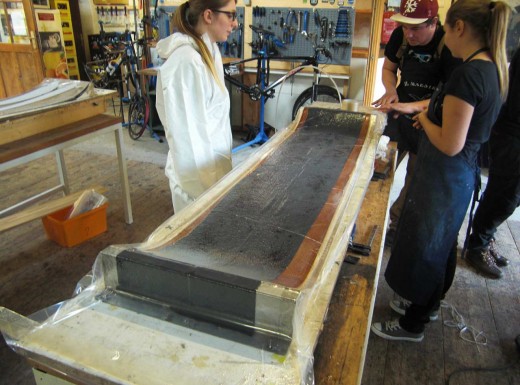
Step 10: Kein Spaß hier! Mit dem Druck von fünf Tonnen, backt der per Schlauch angelegte Unterdruck, die harzversehenen Schichten zusammen © airFreshing.com
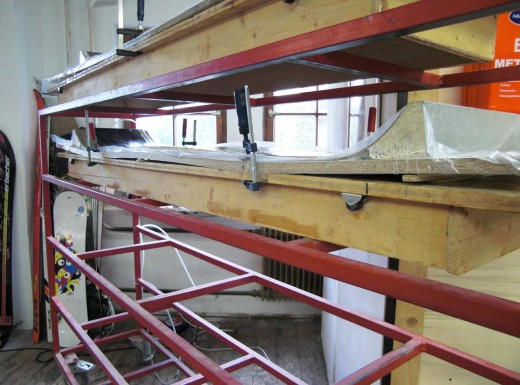
Step 11: Durch Holzleistenunterlagen werden die gewünschten Shapes endgültig erreicht. Über Nacht ruht das Board im Vakuum – alle Schichten können sich in Ruhe verbinden © airFreshing.com
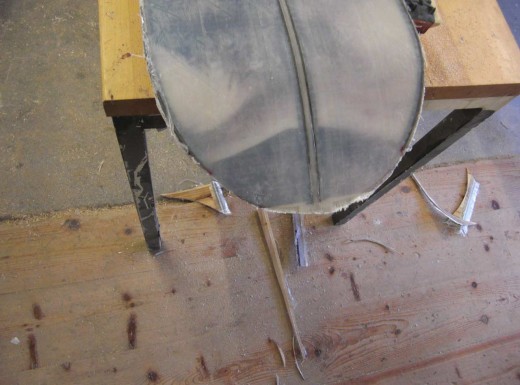
Step 12: Der neu entstandene Rohling wird grob ausgesägt und ab jetzt geshaped © airFreshing.com
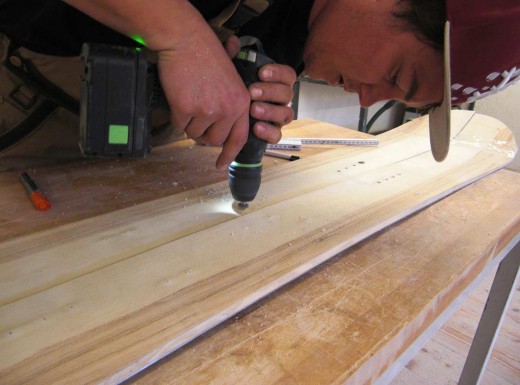
Step 13: die Inserts werden freigebohrt © airFreshing.com
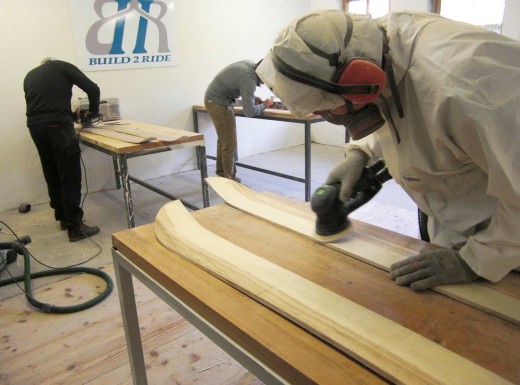
Step 14: Jetzt wird oberflächenveredelt und Überflüssiges weggeschliffen © airFreshing.com
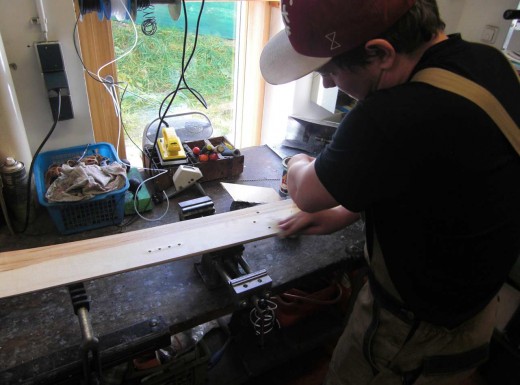
Step 15: Das Board erhält die letzte Ölung © airFreshing.com
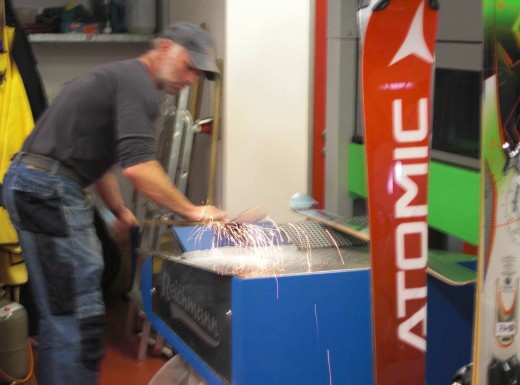
Step 16: Kanten und Belag werden geschliffen © airFreshing.com
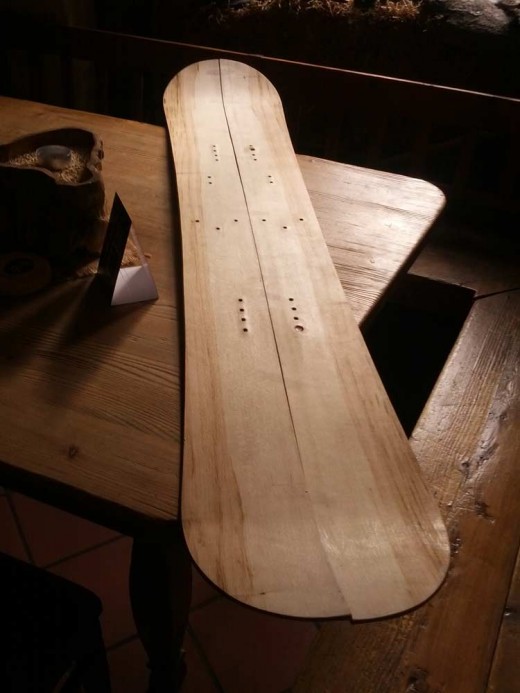
Step 17: Hoch die Tassen, fertig ist das Splitinger! Build2Ride! © airFreshing.com